Dependable Packaging Machine Repair Service for Reliable Operations
Wiki Article
Comprehensive Guide to Effective Packaging Device Repair Work Methods for Optimum Performance
Reliable packaging equipment repair service is vital for maintaining functional connection and product quality in today's busy production setting. Using a structured strategy to diagnostics and repair work, along with precautionary maintenance methods, can considerably enhance device long life and performance.Typical Product Packaging Maker Issues
Product packaging makers, essential for reliable assembly line, typically encounter several usual problems that can interfere with operations. One common trouble is misalignment, which can lead to inappropriate securing or identifying, eventually affecting item integrity and discussion. This misalignment might stem from damaged components or incorrect configuration during preliminary installment.An additional constant problem is inconsistent packaging speeds, often caused by mechanical wear or insufficient maintenance. Irregularity in speed can lead to bottlenecks, causing delays and lowering general performance. Additionally, inadequate training of employees can aggravate these problems, as operators might not completely understand machine capabilities or fixing techniques.
Furthermore, product jams are a common event, usually because of incorrect product specifications or international items blocking the device's course. Such jams can halt manufacturing, demanding prompt intervention to remove the clog and resume procedures.
Last but not least, electronic faults, consisting of software glitches or sensor failings, can restrain equipment performance - packaging machine repair service. These problems require timely interest, as they can result in extended downtime if not dealt with quickly. Comprehending these common concerns is vital for preserving ideal efficiency and reducing disturbances in product packaging operations
Analysis Strategies for Repairs
Carrying out reliable diagnostic techniques is critical for identifying and solving issues in packaging makers. An organized method to diagnostics permits service technicians to determine the origin of malfunctions successfully, therefore minimizing downtime and improving operational efficiency.One of the main techniques entails aesthetic evaluations, where technicians examine the maker for any kind of evident indications of misalignment, wear, or damage. This fundamental action can commonly disclose crucial issues without the need for sophisticated devices. Making use of diagnostic software can greatly boost the troubleshooting process. These devices assess maker performance data, offering insights into anomalies that may not be quickly visible.
Another vital strategy is conducting functional tests. By systematically operating different elements of the device, technicians can observe performance discrepancies, aiding to separate defective parts. In addition, executing vibration analysis and thermal imaging can uncover concealed issues, such as misaligned belts or overheating bearings, which are commonly precursors to extra substantial failures.
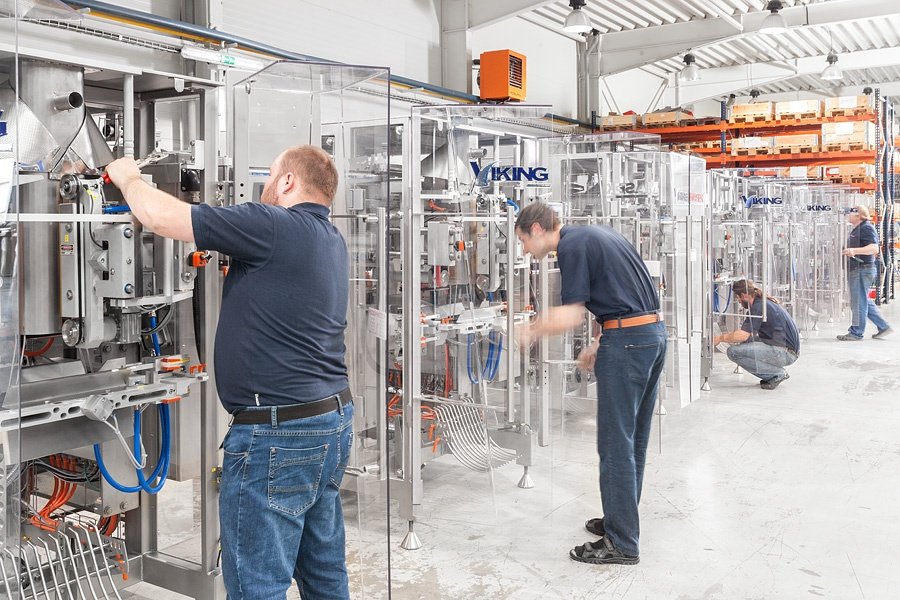
Step-by-Step Repair Procedures
A detailed repair work procedure is vital for bring back functionality to malfunctioning product packaging devices. The process starts with a comprehensive analysis of the problem, utilizing analysis strategies to determine the origin reason of the malfunction. Once recognized, gather the essential tools and replacement components to assist in the repair service.Following, make certain that the maker is powered off and detached from its power source to assure security during the fixing. Recording the machine's configuration prior to disassembly can help in reassembly - packaging machine repair service. Carefully eliminate any kind of covers or panels to access the malfunctioning components, noting any type of details screws or bolts that need attention
Change or fix the defective components according to the supplier's specs, making certain that all links are safe and secure. After reassembly, conduct an aesthetic examination to confirm that all parts are correctly set up which there are no loose links.
When the maker is reassembled, reconnect the power and conduct tests to ensure appropriate capability. Monitor the maker during procedure to determine any kind of residual problems.
Preventive Maintenance Practices
Preserving the capability of product packaging equipments is not only reliant on reactive repair service treatments; positive preventive upkeep methods play a significant role in guaranteeing their longevity and efficiency (packaging machine repair service). By implementing an organized preventative maintenance program, operators can recognize possible problems before they rise into costly malfunctionsSpecialists should consistently examine components such as belts, gears, and sensors for wear and tear. Furthermore, cleaning up machines to remove dirt and debris is crucial for optimum efficiency and to protect against contamination of items.
Training staff on appropriate use and handling of product packaging machines can likewise lessen the threat of operational errors that might lead to devices failure. Establishing an upkeep schedule that consists of routine checks and substitutes of critical parts can substantially prolong the lifespan of the equipment.
Documenting all maintenance tasks not just help in tracking the wellness of the devices however also adheres to governing criteria. By prioritizing precautionary upkeep, companies can have a peek at these guys guarantee their packaging equipments operate at peak efficiency, ultimately boosting efficiency and lowering downtime.
Devices and Resources for Technicians
Furnishing service technicians read this article with the right devices and resources is necessary for efficient packaging maker repair and upkeep. A well-stocked toolkit must consist of precision instruments such as wrenches, screwdrivers, and calipers customized for details device components. Furthermore, analysis devices like oscilloscopes and multimeters allow specialists to recognize electrical problems swiftly and properly.
In addition, purchasing software program remedies for equipment surveillance can improve anticipating upkeep techniques. These applications examine maker performance information, notifying professionals to prospective issues prior to they rise.
Connecting with peers and signing up with industry forums can promote knowledge sharing and finest practices amongst technicians, cultivating a collaborative environment for continuous knowing. Lastly, preserving connections with providers ensures fast accessibility to spare components and specialized devices, reducing downtime throughout repairs. By leveraging these devices and resources, technicians can boost their effectiveness and efficiency in keeping optimum performance of packaging equipments.
Conclusion
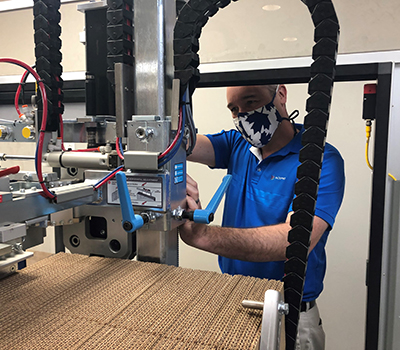
Effective packaging maker repair work is crucial for maintaining operational connection and product top quality in today's hectic production setting.Product packaging makers, important for reliable manufacturing lines, usually experience several common issues that can disrupt operations.A comprehensive repair treatment is essential for restoring capability to malfunctioning product packaging makers.Outfitting specialists with the right tools and resources is crucial for efficient packaging device fixing and maintenance.In verdict, reliable product packaging maker fixing methods are vital for maintaining optimal efficiency see here now and decreasing functional downtime.
Report this wiki page